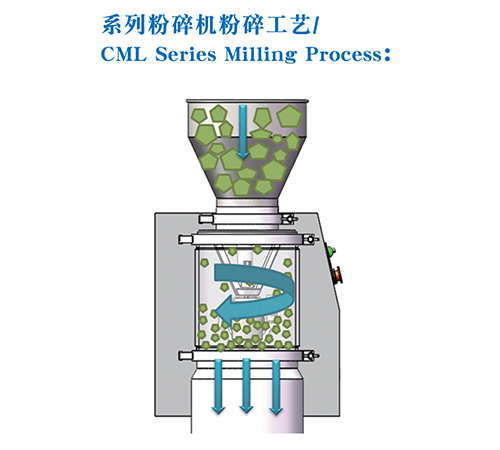
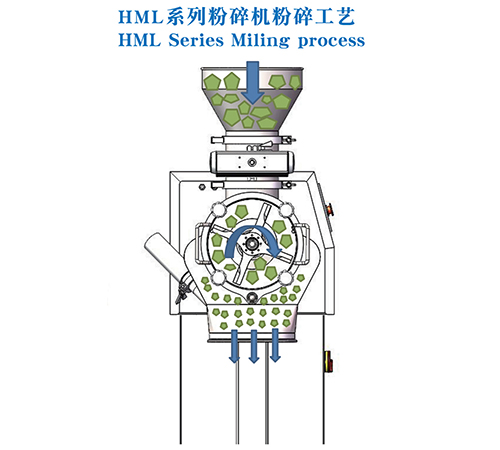
కోన్ మిల్లింగ్
కోన్ మిల్లులు, లేదా శంఖాకార స్క్రీన్ మిల్లులు, ఔషధ పదార్థాల పరిమాణాన్ని ఏకరీతిలో తగ్గించడానికి సాంప్రదాయకంగా ఉపయోగించబడుతున్నాయి.అయినప్పటికీ, వాటిని మిక్సింగ్, జల్లెడ మరియు చెదరగొట్టడానికి కూడా ఉపయోగించవచ్చు.పెద్ద ఫార్మాస్యూటికల్ ప్రాసెసింగ్ కార్యకలాపాలకు ఉపయోగించే పూర్తి-స్థాయి, అధిక-సామర్థ్య యంత్రాల నుండి టేబుల్టాప్ ప్రయోగశాల పరికరాలతో సహా వివిధ పరిమాణాలలో ఇవి వస్తాయి.
కోన్ మిల్లుల ఉపయోగాలు మారుతూ ఉండగా, వాటిని ఫార్మాస్యూటికల్స్లో ఉపయోగించే ధోరణిలో ఉత్పత్తి సమయంలో ఎండిన పదార్థాలను డి-లంపింగ్ చేయడం;ఎండబెట్టడానికి ముందు తడి గ్రాన్యులేటెడ్ కణాల పరిమాణం;మరియు పొడి గ్రాన్యులేటెడ్ రేణువులను ఎండిన తర్వాత మరియు మాత్రలు వేయడానికి ముందు వాటిని పరిమాణీకరించడం.
ఇతర మిల్లింగ్ సాంకేతికతలతో పోలిస్తే, కోన్ మిల్లు ఔషధ తయారీదారులకు ఇతర నిర్దిష్ట ప్రయోజనాలను కూడా అందిస్తుంది.ఈ ప్రయోజనాలలో తక్కువ శబ్దం, మరింత ఏకరీతి కణ పరిమాణం, డిజైన్ సౌలభ్యం మరియు అధిక సామర్థ్యం ఉన్నాయి.
నేడు మార్కెట్లో ఉన్న అత్యంత వినూత్నమైన మిల్లింగ్ సాంకేతికత ఎక్కువ నిర్గమాంశ మరియు ఉత్పత్తి పరిమాణం పంపిణీని అందిస్తుంది.అదనంగా, అవి వేరియబుల్ జల్లెడ (స్క్రీన్) మరియు ఇంపెల్లర్ ఎంపికలతో అందుబాటులో ఉన్నాయి.తక్కువ-సాంద్రత కలిగిన పదార్థాలతో ఉపయోగించినప్పుడు, జల్లెడ స్ట్రెయిట్ బార్లతో రూపొందించబడిన మిల్లులతో పోలిస్తే 50 శాతం కంటే ఎక్కువ నిర్గమాంశను పెంచుతుంది.కొన్ని సందర్భాల్లో, వినియోగదారులు గంటకు 3 టన్నుల వరకు యూనిట్ ఉత్పత్తి సామర్థ్యాన్ని సాధించారు.
డస్ట్-ఫ్రీ కోన్ మిల్లింగ్ సాధించడం
మిల్లింగ్ దుమ్మును ఉత్పత్తి చేస్తుందని అందరికీ తెలుసు, ఇది దుమ్మును కలిగి ఉండకపోతే ఆపరేటర్లకు మరియు ఫార్మాస్యూటికల్ ప్రాసెసింగ్ వాతావరణానికి ముఖ్యంగా ప్రమాదకరం.ధూళిని అరికట్టడానికి అనేక పద్ధతులు అందుబాటులో ఉన్నాయి.
బిన్-టు-బిన్ మిల్లింగ్ అనేది కోన్ మిల్లు ద్వారా పదార్థాలను అందించడానికి గురుత్వాకర్షణపై ఆధారపడే పూర్తి ఇన్-లైన్ ప్రక్రియ.సాంకేతిక నిపుణులు ఒక బిన్ను మిల్లుకు దిగువన ఉంచుతారు మరియు నేరుగా మిల్లుకు పైన ఉంచిన డబ్బాను మిల్లులోకి పదార్థాలను విడుదల చేస్తారు.గురుత్వాకర్షణ పదార్థం మిల్లింగ్ తర్వాత నేరుగా దిగువ కంటైనర్లోకి వెళ్లడానికి అనుమతిస్తుంది.ఇది ఉత్పత్తిని ప్రారంభం నుండి ముగింపు వరకు ఉంచుతుంది, అలాగే పదార్థాన్ని మిల్లింగ్ తర్వాత సులభంగా బదిలీ చేస్తుంది.
మరొక పద్ధతి వాక్యూమ్ బదిలీ, ఇది కూడా ఇన్-లైన్ ప్రక్రియ.ఈ ప్రక్రియ ధూళిని కలిగి ఉంటుంది మరియు కస్టమర్లు అధిక సామర్థ్యాన్ని మరియు ఖర్చును ఆదా చేయడంలో సహాయపడటానికి ప్రక్రియను ఆటోమేట్ చేస్తుంది.ఇన్-లైన్ వాక్యూమ్ బదిలీ వ్యవస్థను ఉపయోగించి, సాంకేతిక నిపుణులు కోన్ యొక్క చ్యూట్ ద్వారా పదార్థాలను ఫీడ్ చేయగలరు మరియు వాటిని మిల్లు యొక్క అవుట్లెట్ నుండి స్వయంచాలకంగా లాగవచ్చు.అందువలన, ప్రారంభం నుండి ముగింపు వరకు, ప్రక్రియ పూర్తిగా మూసివేయబడుతుంది.
చివరగా, మిల్లింగ్ సమయంలో చక్కటి పొడులను కలిగి ఉండేలా ఐసోలేటర్ మిల్లింగ్ సిఫార్సు చేయబడింది.ఈ పద్ధతిలో, కోన్ మిల్లు ఒక వాల్ ఫిక్సింగ్ ఫ్లాంజ్ ద్వారా ఒక ఐసోలేటర్తో కలిసిపోతుంది.కోన్ మిల్లు యొక్క అంచు మరియు కాన్ఫిగరేషన్ ఐసోలేటర్ వెలుపల ఉన్న ప్రాసెసింగ్ ప్రాంతం ద్వారా కోన్ మిల్ హెడ్ యొక్క భౌతిక విభజనను అనుమతిస్తుంది.ఈ కాన్ఫిగరేషన్ గ్లోవ్ బాక్స్ ద్వారా ఐసోలేటర్ లోపల ఏదైనా శుభ్రపరచడాన్ని అనుమతిస్తుంది.ఇది దుమ్ము బహిర్గతమయ్యే ప్రమాదాన్ని తగ్గిస్తుంది మరియు ప్రాసెసింగ్ లైన్ యొక్క ఇతర ప్రాంతాలకు దుమ్ము బదిలీని నిరోధిస్తుంది.
హామర్ మిల్లింగ్
సుత్తి మిల్లులు, కొంతమంది ఫార్మాస్యూటికల్ ప్రాసెసింగ్ తయారీదారులచే టర్బో మిల్లులు అని కూడా పిలుస్తారు, ఇవి సాధారణంగా పరిశోధన మరియు ఉత్పత్తి అభివృద్ధికి, అలాగే నిరంతర లేదా బ్యాచ్ ఉత్పత్తికి అనుకూలంగా ఉంటాయి.డ్రగ్ డెవలపర్లకు కష్టతరమైన APIలు మరియు ఇతర పదార్ధాల యొక్క ఖచ్చితమైన కణ తగ్గింపు అవసరమయ్యే సందర్భాలలో వారు తరచుగా పని చేస్తారు.అదనంగా, సుత్తి మిల్లులు విరిగిన మాత్రలను సంస్కరించడం కోసం పొడిగా చేయడం ద్వారా వాటిని తిరిగి పొందేందుకు ఉపయోగించవచ్చు.
ఉదాహరణకు, తనిఖీ చేసిన తర్వాత, కొన్ని తయారు చేయబడిన టాబ్లెట్లు వివిధ కారణాల వల్ల కస్టమర్ యొక్క ప్రమాణాలకు అనుగుణంగా ఉండకపోవచ్చు: తప్పు కాఠిన్యం, పేలవమైన ప్రదర్శన మరియు అధిక బరువు లేదా తక్కువ బరువు.ఆ సందర్భాలలో, తయారీదారులు మెటీరియల్పై నష్టాన్ని తీసుకోకుండా టాబ్లెట్లను తిరిగి వాటి పొడి రూపంలోకి మార్చడాన్ని ఎంచుకోవచ్చు.టాబ్లెట్లను మళ్లీ మిల్లింగ్ చేయడం మరియు వాటిని తిరిగి ఉత్పత్తిలోకి ప్రవేశపెట్టడం వల్ల చివరికి వ్యర్థాలు తగ్గుతాయి మరియు ఉత్పాదకత పెరుగుతుంది.టాబ్లెట్ల బ్యాచ్ స్పెసిఫికేషన్లకు అనుగుణంగా లేని దాదాపు అన్ని పరిస్థితులలో, తయారీదారులు సమస్యను అధిగమించడానికి సుత్తి మిల్లును ఉపయోగించవచ్చు.
హామర్ మిల్లులు 1,000 rpm నుండి 6,000 rpm వరకు వేగంతో పనిచేయగలవు, అదే సమయంలో గంటకు 1,500 కిలోగ్రాముల వరకు ఉత్పత్తి చేస్తాయి.దీనిని సాధించడానికి, కొన్ని మిల్లులు ఆటోమేటిక్ రొటేటింగ్ వాల్వ్తో అమర్చబడి ఉంటాయి, ఇది మిల్లింగ్ చాంబర్ను మిల్లింగ్ చాంబర్ను ఓవర్ఫిల్ చేయకుండా సమానంగా నింపడానికి సాంకేతిక నిపుణులను అనుమతిస్తుంది.ఓవర్ఫిల్ను నిరోధించడమే కాకుండా, ప్రక్రియ పునరావృతతను పెంచడానికి మరియు ఉష్ణ ఉత్పత్తిని తగ్గించడానికి ఇటువంటి ఆటోమేటిక్ ఫీడింగ్ పరికరాలు మిల్లింగ్ చాంబర్లోకి పౌడర్ ప్రవాహాన్ని నియంత్రించగలవు.
కొన్ని అధునాతన సుత్తి మిల్లులు ద్వంద్వ-వైపు బ్లేడ్ అసెంబ్లీని కలిగి ఉంటాయి, ఇవి తడి లేదా పొడి పదార్థాల సాధ్యతను పెంచుతాయి.బ్లేడ్ యొక్క ఒక వైపు పొడి పదార్థాలను పగలగొట్టడానికి సుత్తిలా పనిచేస్తుంది, అయితే కత్తి లాంటి వైపు తడి పదార్థాల ద్వారా ముక్కలు చేయవచ్చు.వినియోగదారులు వారు మిల్లింగ్ చేస్తున్న పదార్థాల ఆధారంగా రోటర్ను తిప్పుతారు.అదనంగా, కొన్ని మిల్లు రోటర్ అసెంబ్లీలు నిర్దిష్ట ఉత్పత్తి ప్రవర్తనకు సర్దుబాటు చేయడానికి రివర్స్ చేయబడతాయి, అయితే మిల్లు యొక్క భ్రమణం మారదు.
కొన్ని సుత్తి మిల్లుల కోసం, మిల్లు కోసం ఎంచుకున్న స్క్రీన్ పరిమాణం ఆధారంగా కణ పరిమాణం నిర్ణయించబడుతుంది.ఆధునిక సుత్తి మిల్లులు పదార్థ పరిమాణాన్ని 0.2 mm నుండి 3 mm వరకు తగ్గించగలవు.ప్రాసెసింగ్ పూర్తయిన తర్వాత, మిల్లు స్క్రీన్ ద్వారా కణాలను నెట్టివేస్తుంది, ఇది ఉత్పత్తి పరిమాణాన్ని నియంత్రిస్తుంది.తుది ఉత్పత్తి పరిమాణాన్ని నిర్ణయించడానికి బ్లేడ్ మరియు స్క్రీన్ కలిసి పని చేస్తాయి.
పోస్ట్ సమయం: ఆగస్ట్-08-2022